Should we embrace Japanese Lean Words in Manufacturing?
- Russell Watkins
- Feb 8, 2023
- 7 min read
Updated: Feb 4
Exploring the pros and cons of Atarimae, Waigaya, Kodawari, Kansha and more.
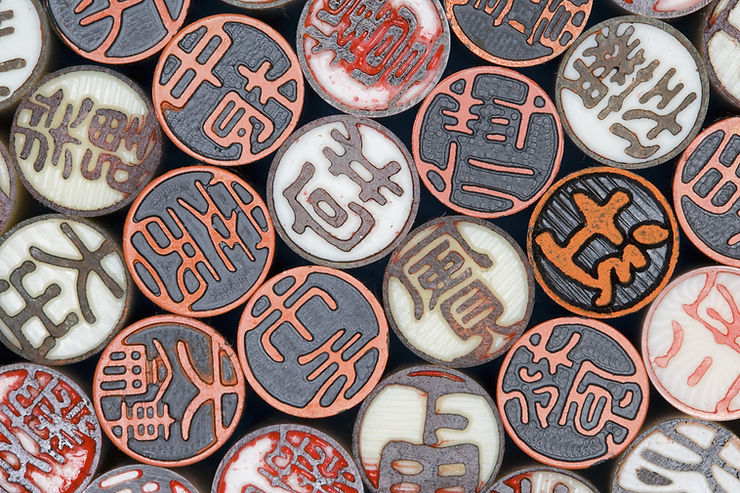
10 Japanese lean words we learned from consulting to Toyota group:
and more importantly we'll explain how they can help you.
We'll get to the 10 Japanese words shortly, but first, we've put a couple of health warnings below to avoid a deluge of salty messages :) By the way, each of the 10 words will be elaborated on in future posts, with a small story to illuminate.
HEALTH WARNING 1:
There's a whole debate in the Lean community about using Japanese words versus steering clear of them. It's a valid debate, we agree that they can be a barrier and become the gated property of a few "experts" in the know, but this isn't the fault of the words themselves. The root of this problem is ego and the desire to look smart. Take this away and the words unfurl to reveal their beautiful simplicity. Indeed, sometimes they can encompass a concept that's not easily translatable.
We'd like to cut through all the scuffling and illuminate 10 of the words that have been most useful in guiding Sempai's lean work, from working with Japanese manufacturers, especially Toyota Group, over the last 20 years.
HEALTH WARNING 2:
This isn't a definitive dictionary description for each of the words, instead, it's a description based on our experience. We’ve worked closely with many Japanese experts in Toyota and beyond but, spoiler alert, we’re not Japanese. We’ve also excluded obvious words like Kaizen (change for the better), Andon (lantern), Heijunka (levelling), and Kanban (pull signal) – although they too are often misunderstood and provide the entry point for useful practices.
WORD 1: ATARIMAE

"Atarimae" are good habits that people develop and practice, as naturally as breathing because they come to believe that they are the right thing to do. These range, at their simplest but most effective, from "not putting parts in a temporary home" or "not putting boxes of parts directly onto the floor" to "minimising the number of objects hanging from the ceiling" when designing a new facility to avoid giving people on the shop floor the oppressive feeling generated by a crowded ceiling.
There is clearly a management responsibility to show the reason and benefits of each atarimae but the basic principle is sound. A rule alone will be followed, generally, for fear of censure and can be guaranteed only if the boss is watching. An atarimae will occur whether the boss is there or not. It is truly voluntary and makes sense, as the boss can't be there all the time to watch everyone. We'd end up with top-heavy management ranks swollen in number to dwarf the value-added group on the shopfloor. Moving from ‘rules’ to ‘atarimae’ isn’t easy and is the result of making them easy to follow and giving people a compelling, sensible reason to bother.
What can you do:
Look at your current ‘rules’ and question the necessity and usefulness. Try to trim them to a manageable number (not easy when SQDC has to be juggled, I know). Rules (beyond non-negotiable safety practices) should be negotiated with those they apply to, otherwise, it's all a bit parent: child again). If there's serious resistance across the board to a rule, it may not be useful or practical.
WORD 2: WAIGAYA

This is a portmanteau word made from 2 Japanese words. Essentially, it's an area in the factory - a physical desk space - that people share ‘openly’ in. Perhaps as a precursor, you've got your local area engineers sat with your operations people, quality people and materials people, so they can all overhear each other's conversations. Waigaya builds on this and has a slightly different meaning. Wai Wai Gaya Gaya essentially means chit-chat. But, in this space, an Operator or a Team Leader can talk openly and honestly without fear of recrimination from a superior. So, it's a safe place to share things, to speak truth to power in a physically anchored space.
What you can do:
Firstly, seating different functions together on the shopfloor is the gift that keeps giving. Secondly, work with the senior people in the area so that they encourage a respectful but open exchange in that physical space. To encourage Waigaya openness, start with how you respond to your reports. People can only model behaviours they can see.
WORD 3: KODAWARI

The translation is “attention to detail”. Look into any high performing team or individual, whether it's manufacturing, elite sports or arts and ‘attention to detail’ will be cited as a reason why they perform so well. It's recognisable in going the extra mile to write a slightly clearer SOP with a better photo, to not just copying and pasting a PFMEA for a similar-ish product but actually looking at the product and process differences to see which new failure modes might be thrown up. Kodawari is so important that we recommend visiting this page, scrolling down and downloading a free pdf copy of "Adventures in Leanland". Flip to chapter 5 and enjoy the next 10 pages or so.
What you can do:
This one's a balance - kodawari is NOT micromanaging your people until they lose their will to live. Read the chapter, jam packed with examples, and see how you can apply it to your manufacturing business. We learned a lot about safety kodawari from working in a construction equipment factory in Shanghai.
WORD 4: KAN KOTSU

Kan refers to our five senses (sight, touch, hearing, smell and taste) and Kotsu is a codified method that helps people learn how to do a tricky task quickly. It’s about recognising the knacks in a job, writing them down and training them to new starters. Doing it well compresses the lead time for people to do a tricky task well and, as a bonus, compresses the range of skill for everyone trained this way. Why wait for people to learn the knacks to a job over time? Combine it with TWI Job Instruction and you've got something close to a superpower.
What you can do:
Ask your Supervisors and Team Leaders to give you names of operators who, if they're away, the Team Leader is nervous because they're the only ones who can do that job really well. Alternatively, look at where your Training/Skills Matrices have poor flexibility - this can be a clue. Anyway, watch one of those jobs and try to unpick the knack - then check whether those knacks are in the SOP and training materials.
By the way - too much knack indicates something different - it likely means that you designed the product or the work poorly and your shopfloor experts are having to use their human ingenuity to overcome the waste you accidentally baked in.
WORD 5: HANSEI
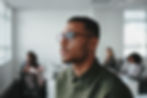
Hansei means restless reflection. When something goes well, we naturally default to celebration and high fives all around. Hansei requires an immediate quiet reflection of ‘what could I/we have done better?’ and ‘what was the gap in my thinking way?’ Hansei doubles your chances to learn, from pure failures, to successes as well. Warning - it's a very restless way to live. There is a balance to be struck here.
What you can do:
Next time a project goes well, pause mid-high five and reflect. Was there any part of this that didn't go as expected - what can we learn from this? This goes back to PDCA and having a plan you check against.
WORD 6: MONOZUKURI

A word often used on its own but is short for “monozukuri wa hito zukuri” or “make good people to make good things”. As in, if you want to run an excellent manufacturing site, invest in your people’s capability. Focus on making good people and then the good things (products) will flow from that.
What you can do:
Start simple. For your Operators, Setters/Technicians, Team Leaders, and Group Leaders. Managers or Engineers - ask this one question: 'What makes an 'Ideal (e.g) Team Leader'" and then mind map or sketch the answer. That's the basis of your monozukuri. Oh and don't do it alone, any one individual has too many biases.
WORD 7: KANSHA / KANSYA
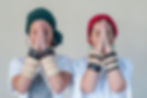
Refers to deep gratitude and is often expressed around a Japanese dinner table in the word “itadakimasu”. It’s the act of giving thanks for the people who grew the food, harvested it, packaged it, transported it to the supermarket and cooked it. It keeps us humble in the factory in remembering that there is a long supply chain of effort to any product. We’re more likely, collectively, to respect the things we produce and be prepared to learn something from these other people.
What you can do:
Start with Quality by treating your scrap and defects as if they were treasure. Expect them to be placed into the defect bin like a baby bird with a broken wing. They want to speak to you and throwing them on top of each other into a packed bin just muddles the conversation. Put the bin front and centre of each section, no hiding. This blog about scrap bins should make it clearer.
WORD 8: KAIKAKU

This is the flip side of the kaizen coin. Where kaizen is about incremental small-step improvements (literally - to change for the better) kaikaku is about periodic innovation leaps upon which kaizen is patiently layered until the next kaikaku.
What you can do:
Assuming that you have a way of generating, harvesting and implementing kaizen ideas, take a step back from your business and look outside. Who among your competitors is most innovative in product and process terms? What can you learn to avoid falling behind? Not all innovation is high cost so don't be put off looking.
WORD 9: KAMISHIBAI
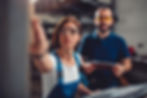
Literally translates as ‘paper drama’ and is used often for TPM or process confirmation T-Card Systems. It’s based on children’s bedtime stories with the entire story on one sheet of paper – like an entire TPM instruction on one T-card or single point lesson. Kamishibai forces brevity and clarity – always a good thing.
What you can do:
Take a look at either (a) your front line TPM tasks or (b) your supervisor confirmation activities and consider whether a visual T-card system might help to manage them better.
WORD 10: JIKOUTEI KAN KETSU (JKK)

JKK refers to Built-in Quality with OWNERSHIP. Jidoka beautifully explains the principle of autonomation (automation with a human touch) stretching back to Sakichi Toyoda’s Type G loom. Unfortunately, our western mantra that “everyone owns quality” has a practical downside resulting in things falling between the cracks (“I thought someone else was doing that bit!”)
JKK essentially means “self-process completion” – I know my exact role and tasks to build in quality and I’m motivated to complete them.
What you can do:
Ask whether you've, in simple words, standardised what the Built-in Quality expectations are of an Operator versus a Setter versus a Team Leader versus a Production Engineer or Quality Engineer. You should be able to identify 3-5 specific "ownerships" for each.
So, there they are; 10 Japanese words that have enlightened Sempai. If you need any help trying or embedding these, give us a call - we've been there and know the way.