2 Lean Skills Your Team Leaders Should Have: Change Points and the 80/20 Rule
- Russell Watkins
- Feb 3
- 3 min read
Updated: Apr 16
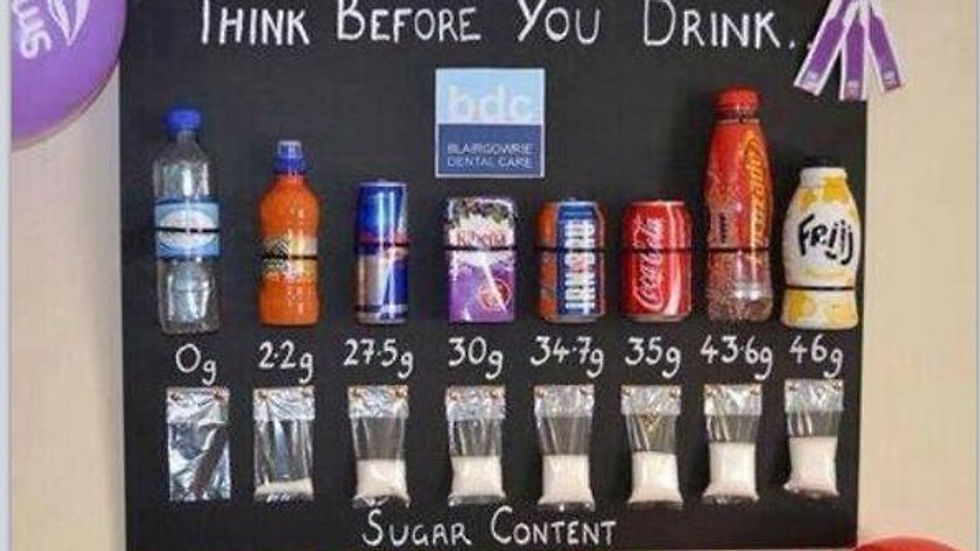
Our blog "2 lean skills your Team Leaders should have: Change Points" discussed one of several simple skills that truly enhance the effectiveness of a Team Leader. In this blog, we will cover another underrated ability: thinking like a long-deceased Italian economist. This approach helps you evaluate your manufacturing operations, whether large or small, and identify the vital few elements that significantly impact performance, relying on the Pareto Principle (or 80/20 rule).
Vilfredo Pareto, although he can't help us in person due to his passing nearly a century ago, left behind the 80/20 rule. This principle continues to guide Team Leaders today.
What is the 80/20 Rule? (Pareto Principle)
Vilfredo Pareto observed that 80% of the land in Italy was owned by just 20% of the population. While this observation may not hold immediate relevance, the implications of this principle are profound. The essence of the 80/20 rule lies in identifying the minority of causes that create the majority of effects.
How Does the 80/20 Pareto Rule Apply in Manufacturing?
As a Team Leader, if you receive pressure to resolve quality issues, understanding that:
Out of 19 part numbers in production, 4 could be responsible for 80% of your scrap.
Among 25 machines, 5 might account for 80% of breakdown losses.
This knowledge can guide your actions effectively.
Implementing the 80/20 Rule in a Fizzy Drink Factory
Consider the dynamics of a fizzy drink canning factory. Instead of aimlessly wandering the production floor, hoping to identify where quality issues arise, you can approach the problem more systematically.
With the 80/20 rule, you could draw a pie chart and a Pareto chart to pinpoint where to focus your efforts. For instance, it may lead you to delve into the orange line of production to address the highest occurrence of defects.


By investigating the orange canning line more closely, you may discover that the issue is linked to "orange dented cans." This targeted focus allows you to tackle a concrete problem effectively.


If you find practical problem-solving challenging, check out our helpful video below for valuable tips and potential pitfalls to avoid.
Key Takeaways for Team Leaders
While the findings may not always fit the exact 80/20 model, this principle has widespread applications. One important lesson is that hand-drawn illustrations facilitate better understanding than overly complex digital spreadsheets. We've encountered many operational leaders who were lost in intricate Excel spreadsheets without grasping the significance of the numbers.
Lack of understanding results in no action, which impedes continuous improvement. To make enduring enhancements, begin by assessing your current status and focus on key issues. After implementing changes, check to see if there's been an impact. This cycle is where data analysis plays a crucial role.
We've even applied 80/20 thinking with Scott, an Operations Manager at an SME who felt overwhelmed with time management. By tracking how he spent his days, we identified several areas for more efficient time use.


The Dangers of Data Analysis
A word of caution: data can be a double-edged sword. Analyzing data should not become an end in itself; the goal is to improve your business. Fifteen years ago, we spoke to one of our Toyota sensei about a rubber molding supplier we were assisting. The supplier had no data collection; thus, we felt unable to help them.
Upon receiving this information through our interpreter, we watched as the sensei went straight to the shop floor. He checked when the scrap bin was last emptied and proceeded to dump rubber defects onto the floor. In front of us, he created a live Pareto chart of parts. "No data?" he asked, demonstrating that sometimes real-life observations speak louder than numbers.
Another day, another lesson. Data is more than just numbers. If you're interested in our blank pie and Pareto pro-formas, contact us through our website here, and we'll happily share them with you.

Comments