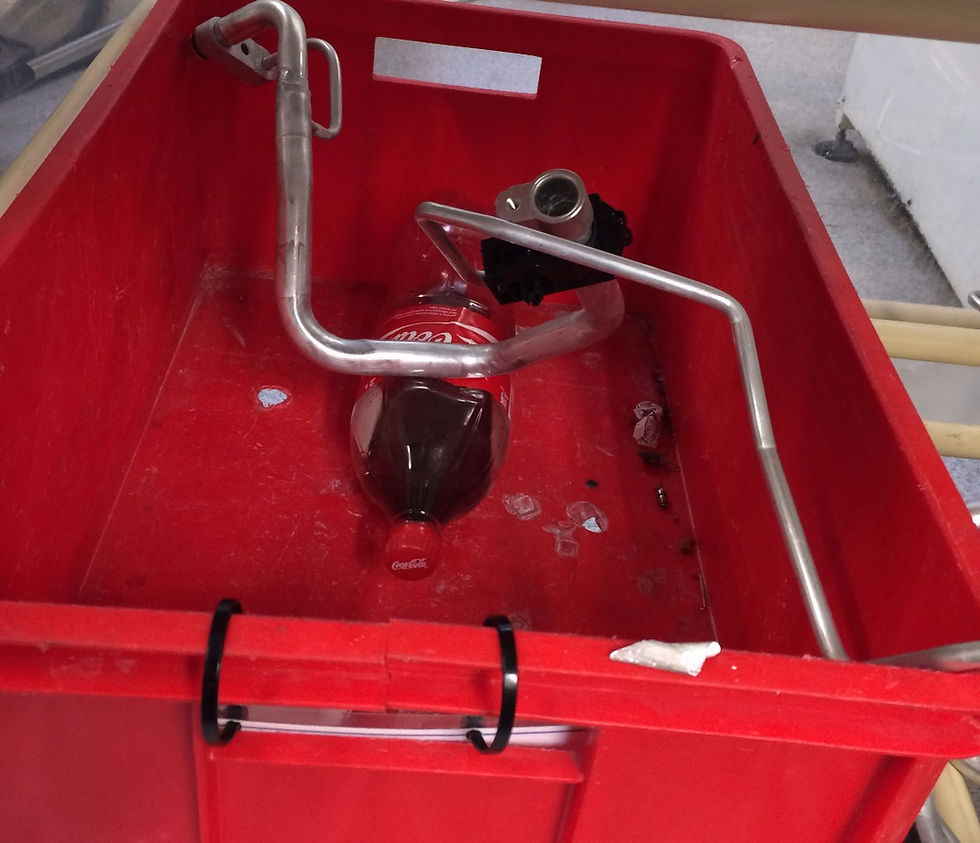
Respect your Scrap & Rework
Twice in a fortnight my annoyance radar sparked into life and beeped furiously as pet hates surfaced in businesses we've supported. We all have pet hates, both at home and in our working lives. The use and misuse of scrap & rework bins does unhelpful things to my blood pressure. I'll not get waylaid differentiating scrap & defect but will simply call them "defect bins" below.
Defects are treasure, not problems - 2 examples
The photo above shows a defect bin in a new Sempai client. Substitute the coke bottle (other waistline threatening carbonated vegetable extract beverages are available) for a crisp packet and you have an identically grim scene that I happened across in a longer term client last week.
These scenes have several things in common, the obvious one being the presence of defects, but this isn't the problem that vexes lean people like me. It's the presence of things other than defects, like coke bottles and crisp packets that stretch our patience.
Each scrap or reworkable part in the defect bin provides an opportunity to surface a hidden problem, learn where we are weak as a business, and fix that problem. The defect part is offering to tell us something to confer a competitive advantage over our deaf-eared competitors. This is why each defect is treasure.
How to love defects as a step towards "Built-in Quality"
The care of defects, to a lean mind, is a significant marker of whether your business has a general preference for Built-in Quality (often called Jidoka) or Inspect-in Quality. Note, that's not simply the quantity of defects, but rather the treatment of them.
Our preference of course is to Build-in Quality & not create defects (one of the 7 wastes), a position most manufacturers incrementally move towards.
So, how should defect bins be treated?
First the obvious stuff. Defect bins, you see, really are treasure chests. Each bin should be:
Small (to fill quickly & force a reaction)
Prominently displayed (problems are opportunities for kaizen)
Be lidless or perhaps transparent (so that a Team Leader or Supervisor can glance into the bin as they patrol their patch to see if defects are building faster or slower than usual, or whether unusual defects are occurring).
Climbing deeper into the defect bin, every defect part should be:
Treated carefully, not left open to further damage by being piled on top of others.
Each should be simply labelled/identified.
These things matter not only to avoid a "bun fight" with suppliers over who actually caused the defect, but to avoid having to diagnose the defect twice upon inspection or at shift end. That's right, the defect bin should be emptied at the end of each shift for ownership of the process and the clarity of starting with a clean slate.
A business that does not look after and display its defects for all to understand & countermeasure is not serious about Built-in Quality. Type "Asaichi" and "lean" - morning market - into your preferred search engine to understand a little more. Crisp wrappers, drinks bottles etc discarded in the bin are, to get all philosophical for a second, disrespectful to those who have gone before. Let me explain...
Kansha (Kansya) - deep gratitude explained
A Japanese friend with a deep lean & Toyota Production System knowledge introduced me some years ago to the concept of "kansha". I'll let him explain to avoid my clumsy interpretation. (He spells it "Kansya" below - in the Japanese style):
"This is the word “kansya” or thanks. Maybe you know Japanese people say “itadakimas” before having a meal. This is the word expressing thanks not only for a person who cook the meal, but also for people who grow rice and natural conditions that allow us to have a meal. So Japanese parents reason with a child that “Don't forget to express your gratitude” (maybe not “express” but “have”). If we can always have kansya in our mind, we can try to learn something from others"
What has this got to do with Quality problems?
Let's go back to those metal defects in the picture at the start of this blog. Each of those parts has been:
Mined & extracted
from ore mined from our finitely resourced planet by geologists, miners & engineers.
Transported & processed
by drivers, various times, to be processed to the point where our business can use them
Moved internally & worked on
others in our business have brought them line-side, processed and added value to them.
The least we owe these people and our planet, in terms of kansha, is to look after them AND to understand those instances where all of that effort has unfortunately come to nothing.
Not to mention the 'kansha' we owe to whatever or whoever created the defect, for the opportunity to solve the problem and grow our own capability (assuming of course that that this person/process is not repeatedly offering us the same opportunity!)
In this sense, respect-for-defects is a subset of respect-for-people. So please have your kansha and treat each defect like a 'baby bird with a broken wing'
7 Wastes defects care - The take-away
This one's easy; put your defect & scrap bins beside the aisle, facing outwards, with no lid so that all can see them without breaking step, searching or having to ask a question. Make it so that there are no excuses to walk past a filling/filled defect bin
Comments